The efficient solution for controlled particle drying
Fluidized bed drying is the optimal method for controlled, gentle and even drying of wet solids. The intensive heat/mass exchange of the
Fluidized bed drying
The efficient solution for controlled particle drying
Fluidized bed drying is the optimal method for controlled, gentle and even drying of wet solids. The intensive heat/mass exchange of the fluidized bed product makes this method particularly effective and time-saving. The technology is also suitable for post-drying of spray granulated or extruded products with very low residual moisture.
Fluidized bed drying can be used in the entire powder processing industry. In the pharmaceutical industry, this innovative method has replaced the time-consuming tray drying long ago: The drying process with fluidized bed drying reduces the drying time in the drying oven by approximately twenty times. In addition, fluidized bed drying provides controlled and uniform drying conditions compared to the uneven drying in trays.
No matter whether the product was produced in the fluidized bed or a high-shear mixer, whether in batch or continuously: With fluidized bed drying, it must be ensured that drying always takes place in a thermodynamic equilibrium. The inlet air temperature must be selected such that only so much moisture evaporates from the surface of the granulate as is transported through the capillaries from the interior of the granulate to the surface. If the inlet air temperature is too high, a surface crust will most likely form which will hamper or even prevent the moisture being transported from deeper layers to the outside. This will delay the entire drying process rather than accelerate it.
For the process variants spray granulation, spray agglomeration or spray coating, it should be noted that not only the moisture needs to evaporate until it has reached a defined residual value, but also that drying takes place during the entire spray process. Too high inlet air temperatures can lead to insufficient liquid bridges, instable granulate structures or inhomogeneous looking films.
Properly used, fluidized bed drying provides an efficient solution for the gentle and even drying of your product.
Fluidized Bed Granulator
Fluidized bed granulator is one of the commonly used processing equipment in the pharmaceutical industries. It is a multi-purpose equipment in that mixing, granulation and drying are all carried out in the same equipment. The equipment operates in a bubbling bed regime.
Parts of a fluidized bed granulator
The main parts of any fluidized bed granulator which may have different design options, following the direction of fluidization gas flow includes;
- Gas plenum (Gas inlet chamber) which screws as the receiver for inlet fluidization air.
- Gas distribution.
- Product container.
- An expanded chamber containing a set of filter bag in the expansion chamber.
- Binders spray system which is usually characterized by one of four nozzle designs.
Nozzle designs of a fluidized bed granulator
- Pressure nozzle –This type of nozzle breaks up fluid under pressure by its inherent instability and its impact on the atmosphere, one another jet or on a fixed plate.
- Rotating nozzle – This nozzle type is also known as rotary atomizer and it is used mainly in spray drying application.
iii. Airless spray nozzle – With this type of nozzle, the fluid is separated into two streams that are brought back together at the nozzle orifice, whereupon impingement form drops.
- Gas atomizing nozzle –This is equally known as two-fluid nozzle. With this nozzle, the binder solution (one fluid) is atomized by compressed air (the second fluid). It is the most commonly used nozzle for fluid bed granulation.
Factors that influence spray nozzle selection
Different designs can be selected for individual main parts of a fluidized bed granulator and this depends on;
- Processing option.
- Mode of operation (batch or continuous).
- Principle of processing.
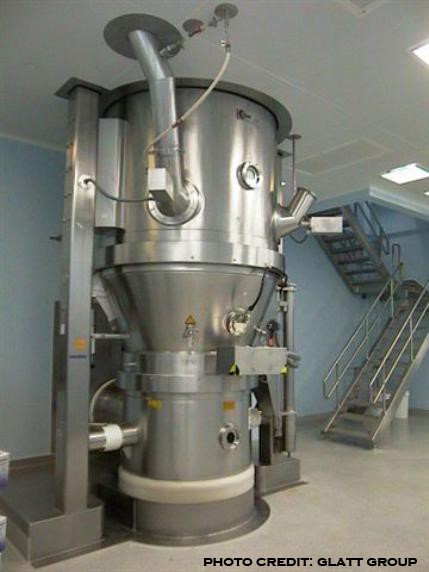
Conventional fluidized bed granulator can be operated depending on the position of the spray system in either “top” for top-spray fluidized bed granulator or “bottom” for bottom spray fluidized bed granulator.
Fluidized bed granulator, in general, is not different from industrial fluidized bed coating equipment except that the spraying zone occupies a large portion of the bed, and also gas velocities used are somewhat similar.
Granulation in a fluidized bed granulator is achieved by suspending the powder in the air of the fluidized bed and then spraying the binder solution from nozzles that are either positioned above or below the powder bed depending on the type of the granulator.
Advantages of Fluidized-Bed Granulator
- Fluidized bed granulator is a one-unit system and thus saves labor cost, transfer loss, and time.
- Heat transfer in fluidized bed granulator is 2 – 6 times greater than that generated by tray dryer.
- The process can be automated once parameters are optimized.
- Drying occurs uniformly and the process prevents mottling.
Disadvantages of Fluidized-Bed Granulator
- It is practicable impossible to achieve the same degree of densification while using fluidized bed granulator in batch mode.
- The equipment is characterized by long resident time.
- There is need for relatively high amount of granulating liquid.
- Fluidized bed granulator is expensive to acquire.
- There is tendency of filter clocking, demising, electrostatic charge, and solvent explosion is high.
- it also produces low-density granules.
References
- Dilip M. Parikh (2010). Handbook of Pharmaceutical Granulation Technology, Third Edition. CRC Press, Taylor and Francis Group, LLC.
- Gilbert, S. B and Christopher, T. R. (2003). Modern Pharmaceutics.CRC Press, Taylor and Francis Group, LLC.
- Isaac, G. and Charles, M. (2003). Pharmaceutical Extrusion Technology. Marcel Dekker, Inc., Basel, New York.
- Jim Litster, and Bryan Ennis (2004). The Science and Engineering of Granulation Processes. Kluwer Academic Publishers, Dordrecht, Netherland.
- Larry, L. A. and Stephen, W. H. (2008), Pharmaceutical Dosage Form: Tablet.CRC Press, Taylor and Francis Group, LLC.
- Namdeo Shinde, Nagesh Aloorkar, Ajit Kulkarni, Bhaskar Bangar, Suyog Sulake, and Pratik Kumbhar (2014). Recent Advances in Granulation Techniques. Asian Journal of Pharmaceutical Sciences.4(1): 38-47.
Fluidized Bed Dryer
Fluidized bed dryer (also called fluid bed dryer) is a kind of equipment used extensively in the pharmaceutical industries to reduce the moisture content of pharmaceutical powder and granules. The equipment works on a principle of fluidization of the feed materials.
In fluidization process, hot air is introduced at high pressure through a perforated bed of moist solid particulate. The wet solids are lifted from the bottom and suspended in a stream of air (fluidized state). Heat transfer is accomplished by direct contact between the wet solid and hot gases. The vaporized liquid is carried away by the drying gasses. Sometimes to save energy, the exit gas is partially recycled.
A typical fluidized bed dryer consists of the following components
- Air preparatory unit.
- Product container.
- Exhaust filter.
- Exhaust blower.
- Control panel.
- Air distribution plate.
- Spray nozzle.
- Solution deliver.
The choice of distributor used during and drying process apart from ensuring uniform and stable fluidization also prevents
- Poor fluidization quality of solids in certain regions in the fluidized bed dryer.
- Plugging of distributor –perforated holes.
- Solids from dropping into wind box or gas plenum located beneath the fluidized bed.
The pressure drops across the distributor must be high enough to ensure good and uniform fluidization.
Parameters to be controlled in fluidized bed dryers (system)
In order to improve operation, efficiency, and reproducibility of a fluidized bed dryer, some parameters need to be controlled. These parameters are categorized into:
- Apparatus parameters: Those controlled by the equipment.
- Process parameters: Those controlled by the process.
- Product parameters: Those controlled by the product.
1. Apparatus/Equipment Parameter
- Position of the air distribution plate: This parameter influences the pattern.
- Shape of the instrument: The annular based design gives a better product.
- Nozzle height:Nozzle height plays a vital role when fluidized bed dryers are used as a coating machine. The atomized coating solution should not get dried before reaching the tablet surface.
2. Process/Operating Parameter
- Temperature: Increased temperature leads to increased moisture diffusivity and hence increased drying rate and decreased drying time. The nature of the material plays an important role in choosing the operating temperature.
- Humidity:Faster drying is achieved when the moisture content of the inlet air is maintained at its minimum.
- Airflow rate/gas velocity: Increasing gas velocity increases drying rate but should be maintained at an optimized rate (not to fast or too slow). Gas velocity has no effect on particles with high internal resistance to moisture transfer.
3. Product Parameters
- Moisture content of the feed material.
- Feed rate/batch size.
- Product moisture content.
- Particle size, shape, and diameter.
Types of Fluidized-Bed Dryers
There are various types of fluidized bed dryer and an individual’s familiarity with the specific characteristics of these various types enables one to make a logical and cost-effective selection of fluidized bed dryer for a drying operation.
In many instances, several different types may provide similar performance at the same cost. It should be noted also that not all modified fluidized bed dryers are necessarily better than the conventional dryers in terms of product quality, or energy efficiency, or drug performance.
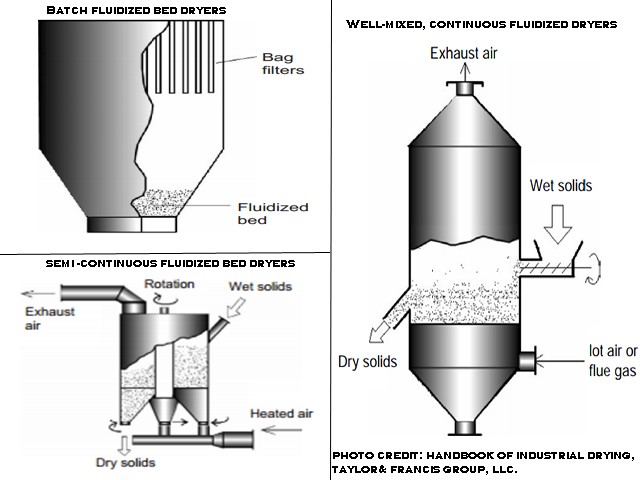
1. Conventional Fluidized Bed Dryers
Conventional fluidized bed dryers include;
- Batch fluidized bed dryers.
- Semi-continuous fluidized bed dryers.
- Well-mixed, continuous fluidized dryers.
- Plug flow fluidized bed dryer.
2. Modified Fluidized Bed Dryers
Various types of modified fluidized bed dryers have been developed and are applied in many industrial processes to overcome some of the problems encountered while using conventional fluidized bed dryers for a drying process. They include but not limited to;
- Hybrid fluidized bed dryers
- Pulsating fluidized bed dryers
- Fluidized bed dryer with immersed heat exchange.
- Mechanically assisted fluidized bed dryer.
- Vibrated fluidized bed dryer.
- Agitated fluidized bed dryer/swirl fluidizers.
- Fluidized bed dryers of inert particles.
- Spouted bed dryer.
- Recirculating fluidized bed dryer.
- Jetting fluidized bed dryer.
- Superheated steam fluidized bed dryer.
- Fluidized bed freeze dryer.
- Heat pump fluidized dryers.
It should be noted that not all modified fluidized bed dryers are necessarily better than the conventional dryers
in terms of product quality, or energy efficiency, or drying performance.
Advantages of Fluidized-bed Dryers
- High rates of moisture removal due to excellent gas-particle constant which results in high heat and mass transfer rates.
- High thermal efficiency is usually achieved if part of the thermal energy for drying is supplied by the internal heat exchanger
- Lower capital and maintenance cost
- Reduced contact time for drying.
- Ease of control.
Disadvantages of Fluidized Dryers
- High pressure drops results as a result of the need to suspend the entire bed in gas which equally leads to high energy consumption.
- Requires increased gas handling due to extensive recirculation of exhaust gas for high thermal efficiency operation.
- Poor fluidization and low flexibility especially if the feed is too wet.
- Not the best choice of equipment when organic solvents need to be removed during drying.
- Non-uniform product quality for certain types of fluidized bed dryers.
- Entertainment of fine particles.
- High potential for attrition; and in some cases agglomeration of fine particles.
- The conventional hot air fluidized bed dryers are not a good choice of dryer when handling toxic or flammable solids since there is danger of fire or explosion of flammability limits are exceeded.
Reference
- Arun S. Mujumdar (2015). Handbook of Industrial Drying. CRC Press, Taylor and Francis Group, New York.