Punches and dies as a key element of the tablet formulation process. They are responsible for the final appearance and shape of the tablets manufactured, so they must be designed and manufactured with great accuracy and care. During operation, tools are exposed to significant static and dynamic forces. They often press abrasive or corrosive powders, which requires the use of high-quality steels, appropriately selected heat treatment, often coating with special coatings to prevent rapid tool wear or tablet sticking, or the use of special materials such as carbides.
Some applications (e.g. household chemicals or effervescent tablets) require the use of plastic inserts, such as Teflon or vulkollan, which further protect the pressing section and are a consumable component that can be replaced. ADAMUS S.A. designs and manufactures punches and dies for tablet presses of all types, according to EU (ISO), IPT (TSM) or specific tablet press manufacturers’ standards, according to customer needs. Our range includes tools for the manufacture of round and shaped tablets, monoblock and foldable, single- and multi-tip tools.
The tools can be supplied in special plastic boxes suitable for later storage. Each batch shipped is accompanied by a measurement record covering 100% of the tools delivered.
Tooling for exotic shaped tablets
With the appropriate design software and the manufacture based on digitally controlled machines, we also provide punches and dies with shapes more complex than those normally used in the pharmaceutical industry.
The only limitation to the variety of these shapes is the strength of the tools and the technological limitations of the tablet formation process. When developing new tablet shapes and forms, we remain open to collaboration, both with the marketing and R&D departments of our customers. The design of 2D and 3D tablets by an experienced team of engineers always takes into account the individual needs and expectations of our customers. Also with them in mind, our proprietary TabGen programme was developed, enabling buyers of products to verify their designs before starting the manufacturing process.
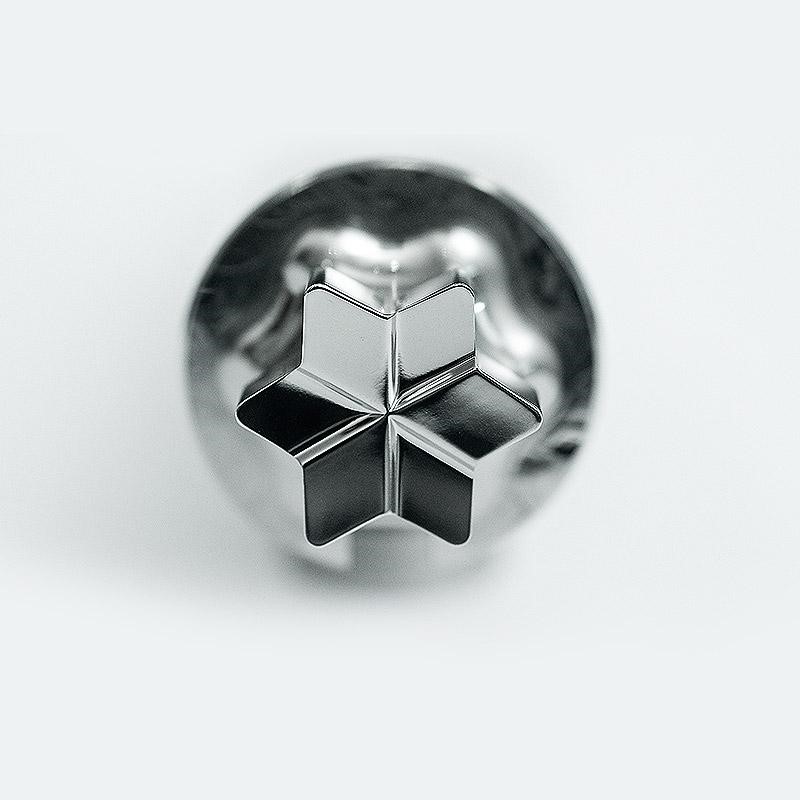
Multi-tip Punch and Dies
Multi-tip tooling applied by ADAMUS S.A. is a cost effective way to significantly increase the capacity of produced tablets without investing in the new tablet presses by reducing:
- labour costs
- maintenance costs
- investment costs
- energy costs
Multi-tipped tooling is available in two different configurations:
- assembly construction – composite
- solid construction – monoblock
The choice between those two options depends on the application, customer requirements, internal cleaning procedures and technical feasibility (the tablet dimensions and number of tips).
By using multi-tipped tooling the number of tablets produced per one turret revolution should be theoretically the multiple of the number of tips in the punch. However, due to the slightly lower turret speed connected with the necessity of the filling of more die holes, the real capacity can sometimes be lower. Depending on the product characteristic the measured capacity increase can vary but the mean values are ca. 1.5 for double-tiptooling, 2.8 for four-tip tooling and 4.5 for six-tip tooling
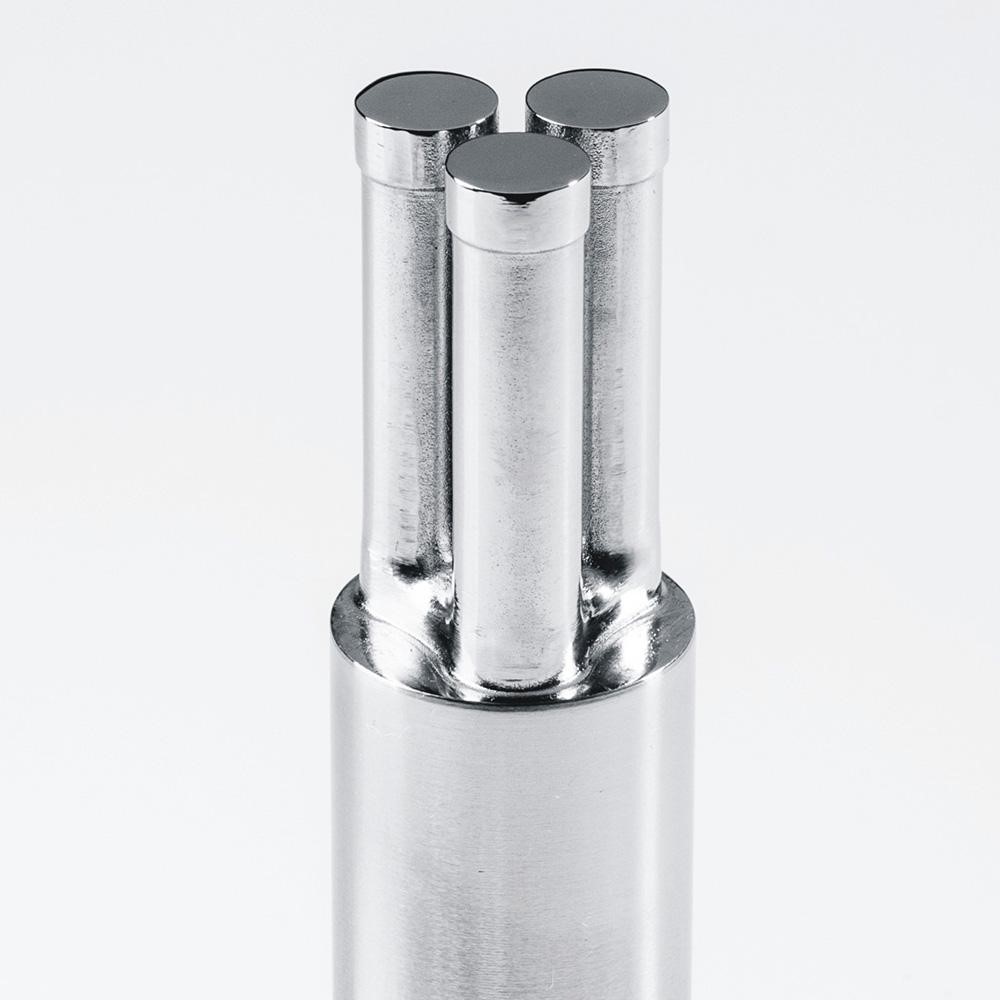
Special Tools
ADAMUS S.A. offers a wide variety of solutions used with regard to special client requirements. This enables us to manufacture top quality special tools.
- punches with rotating heads
- tools made of sintered carbides or tool with ceramic inserts
- large-size tooling
- tools for special tablets with holes (eg. catalysts)
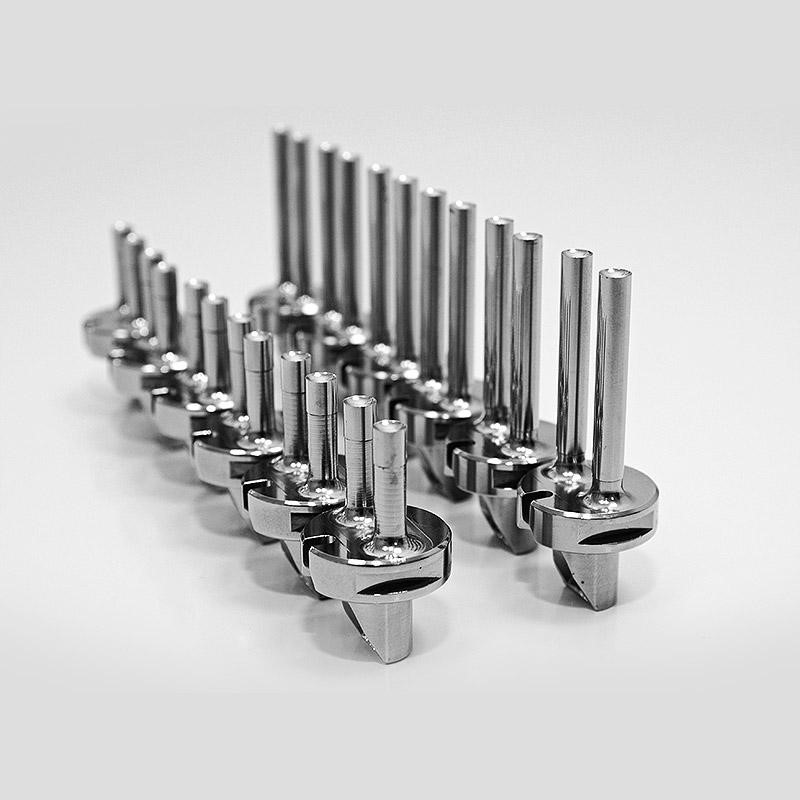
Special Steels
The main requirements for steels used in the manufacturing of compression tooling are the wear resistance, good resistance to chipping, high compressive strength, good through hardening properties, high hardness after high temperature tempering and good stability in hardening.
ADAMUS S.A. uses steel grades which fulfill those requirements and purchase them only from world leading steel producers.
Besides the standard steel grades used by all compression tooling suppliers, ADAMUS S.A. offers a series of different specialty steels which can solve the tableting problems with abrasive, sticky and corrosive products as well as products which requires the higher compression forces than recommended due to the tablet size and dimensions. Such steels with the combination of different coatings, the right surface finish and very narrow dimensional tolerances make the tooling supplied by ADAMUS S.A. one of the best in the world.
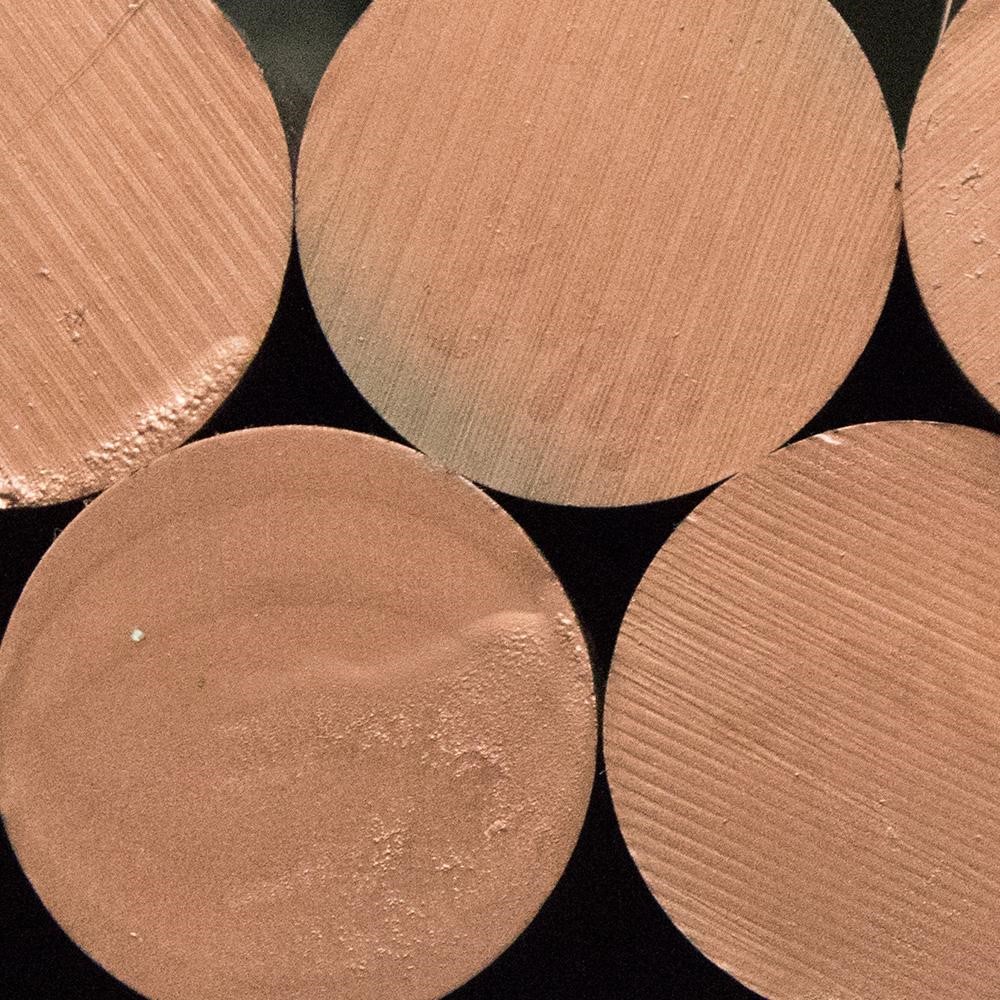
Punch Coating
ADAMUS S.A. is constantly looking for innovative solutions to improve the degree of hardness of the surfaces of tools used in the manufacturing process using substances with different properties. Higher abrasion resistance, reduced coefficient of friction, minimised tendency to tool seizure, and increased corrosion resistance and anti-adhesion properties that eliminate sticking, are the result of our continuous research and development of tool coatings, the quality and durability of which are crucial for our customers.
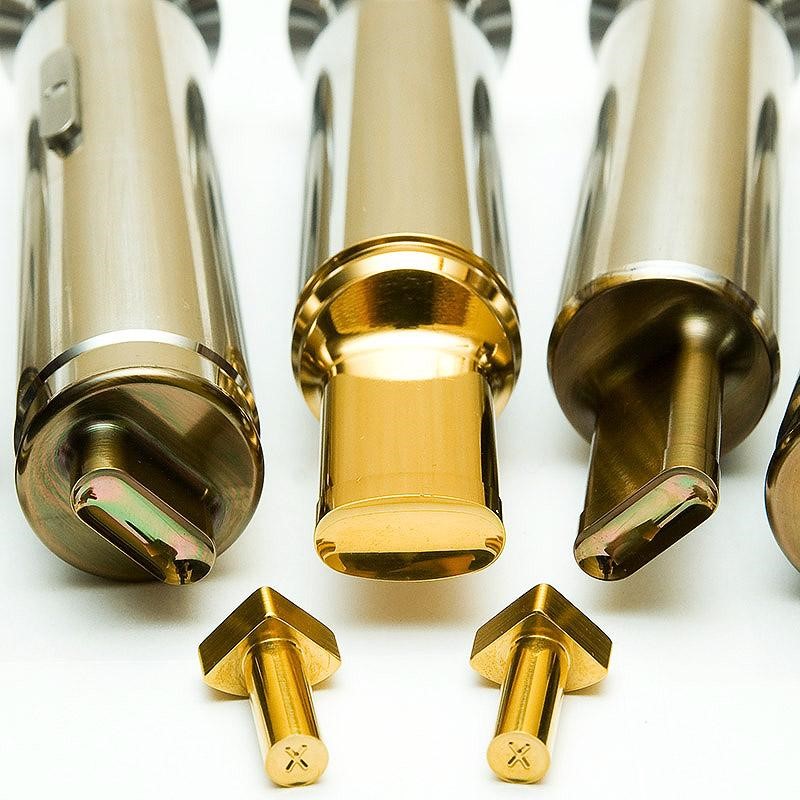
Tablet designing
Various shapes
The company’s rich experience enables it to design tablets of various shapes with different engravings or logos, whilst taking into consideration the maximum durability of the tools used in manufacturing or the final layout of tablets (coating). The first stage of the design process includes the preparation of the tablet image.
Tablet or tool designs
Adamus S.A. is capable of preparing such an image following clients’ instructions or basing it on submitted tablet or tool designs. Furthermore, it is possible to calculate the mass of tablets of a certain shape or a change with the maintenance of the volume. Upon a client’s wish, 3-dimensional visualisations of the designed tablets are prepared.
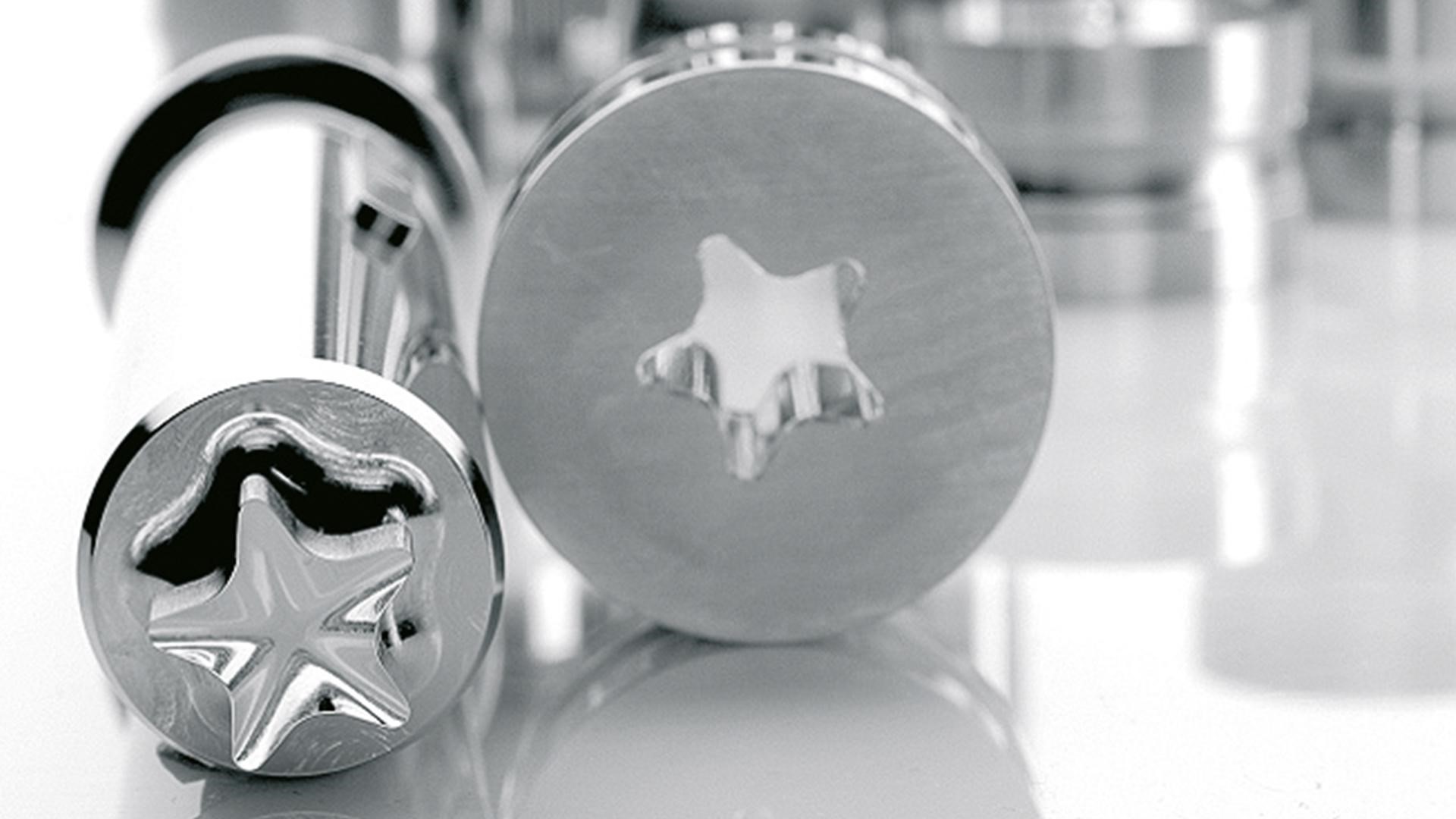